Analysis to optimize the adhesion system for ROMERIN
Analysis to optimize the adhesion system for ROMERIN
To improve the adhesion system, measurements and tests were carried out on the basis of a previous project whose grip system was given by different types of engines: brushless and DC. The stator developed, from which the new systems began to evolve, had several disadvantages: high vibrations and the grip of the engine was too weak.
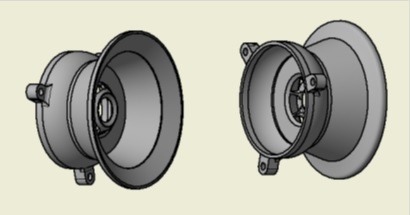
In order to find the best and most efficient model, various experimental tests were carried out which consisted in taking of measures with respect to the following parameters: atmospheric pressure, the revolutions per minute of the rotor and the consumption in amperes of the engine.
Finally, it was concluded that the rotor with the best results in both performance and vacuum achieved is the rotor with double blade centered at the inlet. With these results we started with the stage of design and manufacture, after many iterations solving problems of resonance, vibrations and bad results was designed the final version shown below.
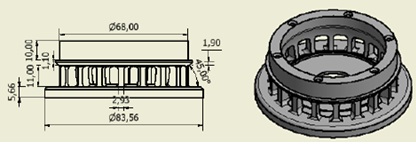
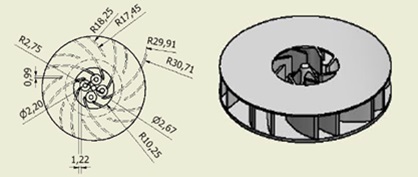
As for electronics, it was necessary to engage a circuit inside the suction cup capable of sensing and checking out the correct performance of the system. The two types of sensors used were:
1. Infrared sensor: Used to measure the distance to the support surface and to indicate when the suction cup is properly sustained, in which case it can begin to vacuum.
2. Barometric sensor: Used to measure atmospheric pressure all the time and to verify that it is making the vacuum properly.
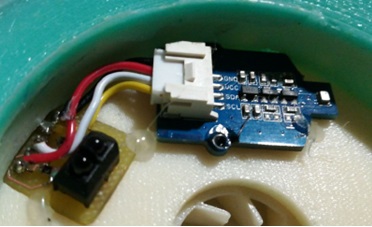