¿Quién ha dicho que las energías renovables no puedan aportar inercia a la red?
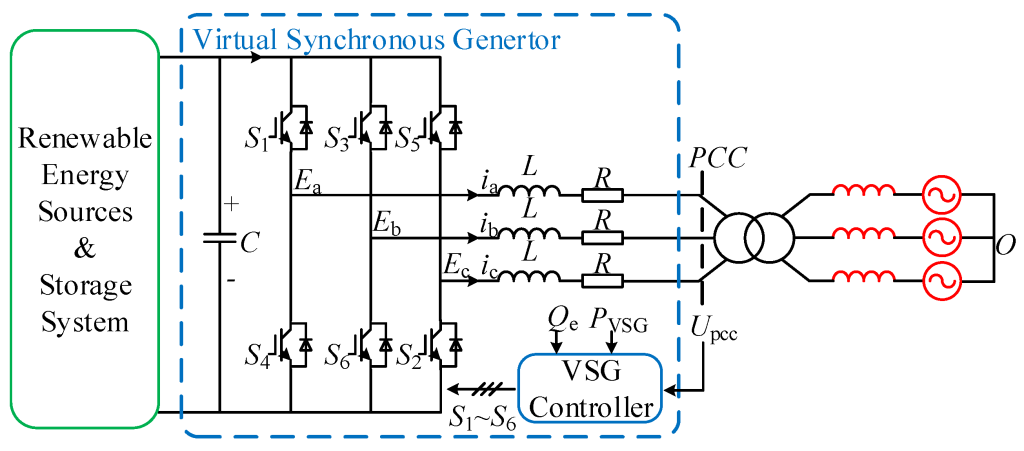
Los generadores síncronos virtuales, también conocidos como sincroconvertidores o máquinas síncronas virtuales, son inversores que imitan el comportamiento de los generadores síncronos tradicionales. Estos dispositivos están diseñados para proporcionar inercia sintética como servicio auxiliar en los sistemas eléctricos de potencia. La inercia es una propiedad fundamental de los generadores síncronos estándar, que se deriva de la masa rotatoria del sistema, la cual gira a una frecuencia proporcional a la electricidad generada. La inercia juega un papel crucial en la estabilidad de las redes eléctricas, ya que la energía cinética de la masa giratoria actúa como un amortiguador frente a los cambios de frecuencia en la red. En contraste, los inversores tradicionales carecen de esta propiedad, ya que la forma de onda que generan se crea de manera artificial mediante la electrónica de potencia.
En un sistema eléctrico, la frecuencia de la red debe mantenerse dentro de un rango estrecho en torno a un valor nominal, generalmente 50 o 60 Hz, dependiendo de la región. Cuando existe un desequilibrio entre la oferta y la demanda de electricidad, la frecuencia de la red se desvía de su valor nominal. Los generadores síncronos, debido a su masa giratoria, tienen la capacidad de proporcionar o absorber energía cinética para contrarrestar estos desequilibrios, lo que ayuda a estabilizar la frecuencia. La inercia de un generador síncrono amortigua los efectos de las oscilaciones de potencia activa, lo que mejora la estabilidad de la frecuencia de la red. Sin embargo, los generadores basados en inversores como interfaz con la red, como los que se encuentran en las energías renovables, carecen de esta inercia física, lo que plantea un desafío para la fiabilidad del sistema eléctrico a medida que aumentan las energías renovables basadas en inversores.
El crecimiento de las energías renovables, especialmente la fotovoltaica (PV) y la eólica, ha incrementado la presencia de inversores en las redes eléctricas. Estos inversores, al no tener inercia, responden rápidamente a los cambios de la red durante los periodos de transitorios, los cuales son comúnmente causados por fallos o cambios abruptos de carga. En estos momentos, la falta de inercia puede empeorar las condiciones de la red, ya que los inversores ajustan su salida de manera casi inmediata, sin la capacidad de amortiguar los cambios como lo hace un generador síncrono. Este fenómeno ha generado preocupaciones sobre la estabilidad del sistema eléctrico, particularmente en regiones donde la penetración de energía renovable es elevada.
Para abordar este desafío, los generadores síncronos virtuales surgen como una solución innovadora. Estos inversores están diseñados para simular la inercia de los generadores síncronos tradicionales al responder a los desequilibrios de frecuencia de la red. A través de un control adecuado, los inversores pueden generar inercia sintética al modificar su par eléctrico, que está relacionado con la tasa de cambio de la frecuencia de la red (RoCoF, por sus siglas en inglés). Esto permite que los inversores participen en el proceso de estabilización de la frecuencia, similar a lo que haría un generador síncrono real.
Sin embargo, para que un generador basado en inversor proporcione una inercia sintética efectiva, debe operar por debajo de su capacidad máxima, reservando una parte de su salida para poder reaccionar a los cambios de frecuencia. Este requisito limita la capacidad total de generación de energía de los inversores, ya que una fracción de su capacidad se dedica exclusivamente a la respuesta de inercia. Además, la variabilidad inherente de las fuentes de energía renovable puede dificultar aún más la capacidad de los inversores para proporcionar una inercia sintética confiable, ya que la producción de energía no es constante.
Un aspecto técnico importante de los generadores síncronos virtuales es su control. Cuando el inversor se controla como una fuente de tensión, requiere un sistema de sincronización que le permita sincronizarse con la red y regular tanto la potencia activa como la reactiva intercambiada con la misma. En este caso, el sistema de sincronización debe proporcionar tanto la frecuencia como la amplitud de la red. Por otro lado, cuando el inversor se controla como una fuente de corriente, la sincronización solo requiere ajustar la fase de la red, lo que facilita el control. Este tipo de control permite integrar la función de sincronización dentro del controlador de potencia, sin necesidad de un sistema de sincronización externo, lo que mejora la eficiencia y la respuesta del sistema.
En conclusión, los generadores síncronos virtuales representan una alternativa prometedora para mitigar los problemas derivados de la falta de inercia en los sistemas eléctricos modernos, especialmente a medida que aumentan las fuentes de energía renovable basadas en inversores. Aunque los inversores tradicionales no tienen inercia física, los sincroconvertidores pueden proporcionar una solución efectiva al emular el comportamiento de los generadores síncronos, mejorando así la estabilidad y fiabilidad de las redes eléctricas. Sin embargo, los desafíos técnicos relacionados con la capacidad de respuesta y la variabilidad de las fuentes de energía deben ser considerados para garantizar que los generadores síncronos virtuales puedan desempeñar un papel crucial en el futuro de la energía renovable.
La revolución de los convertidores de potencia en el sector del transporte
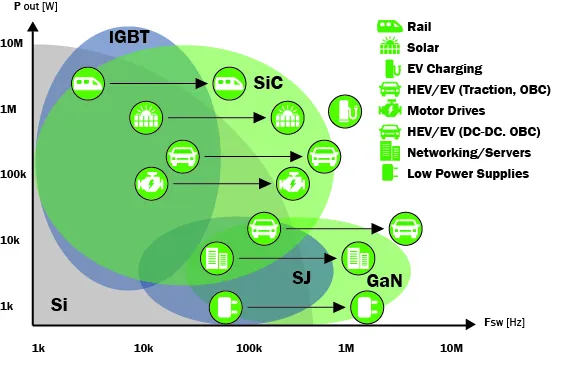
Autores:
Kumar V. Mahtani Mahtani
Profesor Ayudante Doctor en el Departamento de Automática, Ingeniería Eléctrica y Electrónica e Informática Industrial, Universidad Politécnica de Madrid.
Amit Kumar Sharma
Investigador en Indian Institute of Technology Delhi, India.
En la actualidad, el sector del transporte está viviendo una transformación radical, impulsada por la creciente demanda de soluciones más limpias y sostenibles. A medida que los vehículos con motores de combustión interna ceden paso a los vehículos eléctricos e híbridos, se requiere de soluciones tecnológicas que mejoren la eficiencia energética y reduzcan el impacto ambiental. Este cambio es especialmente evidente en aplicaciones de transporte como vehículos eléctricos, ferroviarios y aeronáuticos, donde la electrónica de potencia juega un papel fundamental. En concreto hablaremos de transistores MOSFET. Aquí, los semiconductores de banda prohibida ancha (WBG), como el carburo de silicio (SiC) y el nitruro de galio (GaN), están revolucionando el panorama de la conversión de energía, mejorando la eficiencia, el tamaño y el peso de los sistemas eléctricos.
Propiedades y ventajas de los semiconductores WBG
Los materiales WBG tienen propiedades que los hacen particularmente atractivos para aplicaciones de alta potencia, como las utilizadas en vehículos eléctricos y sistemas de transporte. Comparados con el silicio (Si), los semiconductores WBG como el SiC y el GaN poseen una banda prohibida más ancha, lo que les permite soportar mayores tensiones y temperaturas sin degradarse. El SiC, por ejemplo, tiene una banda prohibida de 3.2 eV, frente a los 1.1 eV del silicio, y su capacidad para soportar mayores tensiones eléctricas lo hace ideal para aplicaciones que requieren de alta fiabilidad en condiciones extremas.

Estas características permiten que los dispositivos basados en SiC y GaN operen a frecuencias de conmutación más altas, lo que a su vez reduce las pérdidas de energía y mejora la eficiencia global del sistema. Además, estos materiales soportan temperaturas de operación más elevadas, lo que les permite funcionar de manera más eficiente sin necesidad de sistemas de refrigeración complejos, reduciendo tanto el peso como el tamaño de los sistemas eléctricos. Este último punto es crucial, ya que en muchas aplicaciones de transporte, especialmente en vehículos eléctricos y ferroviarios, el tamaño y el peso de la electrónica de potencia son factores determinantes.
Aplicaciones en vehículos eléctricos e híbridos
En los vehículos eléctricos e híbridos, la electrónica de potencia tiene un papel fundamental en la conversión de energía para el motor y otros sistemas auxiliares. El inversor de tracción, por ejemplo, convierte la energía de la batería en corriente alterna para alimentar el motor eléctrico. En este caso, el SiC es la opción preferida para inversores de alta tensión, debido a su capacidad para manejar grandes cantidades de energía con menores pérdidas y a su mejor capacidad para operar a temperaturas elevadas. Esto no solo mejora la eficiencia del sistema, sino que también reduce el tamaño y el peso del inversor, lo que es crucial para maximizar la autonomía de los vehículos eléctricos.
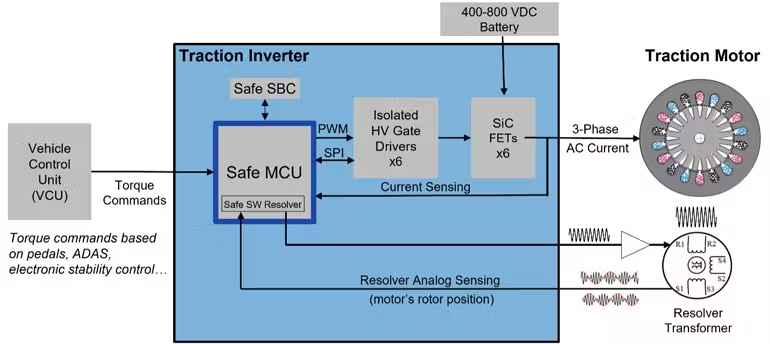
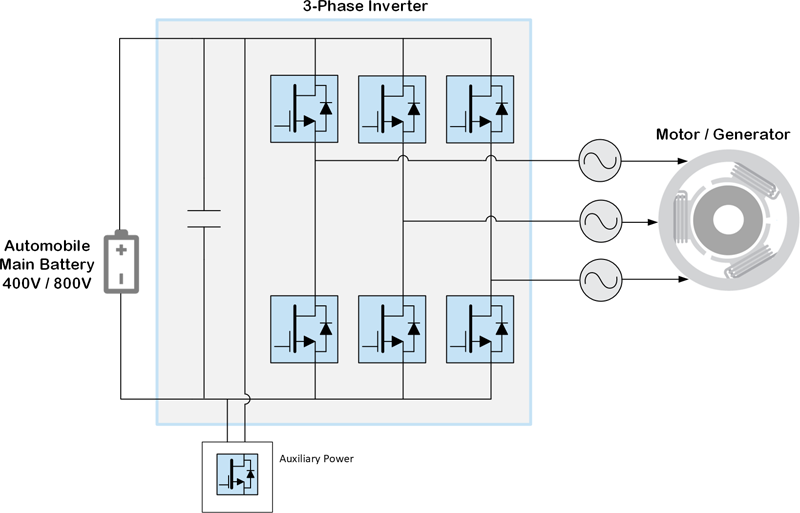
Inversor de tracción de vehículos eléctricos (vista de los elementos de potencia). Fuente: Qorvo.
Además, los cargadores de a bordo (OBC) y los convertidores de corriente continua (CC/CC) son componentes clave que también se benefician del uso de semiconductores WBG. Los OBC convierten la corriente alterna de la red eléctrica en corriente continua para cargar las baterías de los vehículos. Con dispositivos de GaN, la frecuencia de conmutación es mucho más alta, lo que permite reducir las pérdidas de conducción y minimizar el tamaño del sistema, a la vez que mejora la velocidad de carga. Por otro lado, los convertidores de CC/CC de baja tensión, que convierten la energía de la batería a 12 V o 48 V para alimentar los sistemas auxiliares del vehículo, también se benefician de la alta frecuencia de conmutación de estos materiales, lo que reduce aún más el tamaño y el peso de los componentes.
Aplicaciones ferroviarias
En el ámbito ferroviario, la electrónica de potencia es igualmente crítica para la conversión de energía, tanto para el accionamiento de los trenes como para los sistemas auxiliares. Los trenes eléctricos dependen de la conversión de energía en sistemas de tracción, que deben ser altamente eficientes para reducir el consumo de energía y mejorar la fiabilidad operativa. Tradicionalmente, los transistores bipolares de puerta aislada (IGBT) basados en silicio se han utilizado para estos fines, pero los dispositivos de SiC están empezando a reemplazarlos debido a sus mayores capacidades de conmutación y a su mejor gestión térmica.
Los inversores de tracción y auxiliares en trenes requieren operar a alta frecuencia para mejorar la densidad de potencia, reducir las pérdidas y aumentar la eficiencia general del sistema. Con dispositivos basados en SiC, las pérdidas de conmutación y conducción se reducen significativamente, lo que permite que los trenes operen con mayor eficiencia, disminuyendo el consumo de energía y mejorando el rendimiento del sistema de frenado regenerativo. Este tipo de frenado, que convierte la energía cinética de los trenes en energía eléctrica que se puede almacenar o devolver a la red, se ve beneficiado por la mejor gestión de la potencia que ofrecen los semiconductores WBG.
Además, el uso de estos materiales permite una mayor eficiencia en el sistema de refrigeración, dado que los dispositivos pueden operar a temperaturas más altas, lo que reduce la necesidad de grandes sistemas de enfriamiento. Esto, combinado con la alta frecuencia de conmutación, también permite reducir el peso y el volumen de los componentes de potencia, lo que es especialmente valioso en la industria ferroviaria.
Aplicaciones en el sector marítimo y aeronáutico
El sector marítimo también ha experimentado avances significativos gracias al uso de semiconductores de banda prohibida ancha. Los sistemas de propulsión eléctrica en barcos se benefician de la alta eficiencia de conversión de energía de los dispositivos de SiC y GaN, especialmente cuando se trata de sistemas que operan con energía de corriente continua (CC). Estos dispositivos permiten la reducción de tamaño y peso de los convertidores de potencia, lo que se traduce en menores requisitos de espacio y un aumento en la eficiencia del combustible.
En la aviación, la transición hacia sistemas de propulsión híbridos y totalmente eléctricos está impulsando la necesidad de dispositivos de potencia que puedan operar a altas frecuencias de conmutación para mejorar la eficiencia de los generadores y sistemas de conversión de energía. Los dispositivos de SiC están comenzando a reemplazar los basados en silicio debido a su capacidad para manejar tensiones y temperaturas mucho más altos, lo que es crucial para el funcionamiento de generadores y motores en aeronaves. Estos sistemas requieren dispositivos capaces de operar a frecuencias más altas, lo que permite el uso de componentes más pequeños y ligeros, mejorando así el rendimiento general del avión.
En conclusión, la electrónica de potencia está viviendo una verdadera revolución con la integración de semiconductores de banda prohibida ancha como el SiC y el GaN. Estas tecnologías no solo permiten la mejora de la eficiencia en una variedad de aplicaciones de transporte, sino que también contribuyen a la reducción de tamaño y peso de los sistemas, lo que es esencial para cumplir con las crecientes demandas de sostenibilidad y eficiencia energética. El uso de dispositivos de SiC y GaN está permitiendo la creación de vehículos más eficientes, trenes más confiables y barcos y aviones con una conversión de energía más efectiva. Esta transición hacia nuevos materiales semiconductores en la electrónica de potencia promete transformar el sector del transporte, no solo mejorando el rendimiento, sino también ofreciendo soluciones más ecológicas y eficientes para el futuro.
Modos de operación de los variadores de frecuencia: generador, red y aislado.
Autor:
Kumar V. Mahtani Mahtani
Profesor Ayudante Doctor en el Departamento de Automática, Ingeniería Eléctrica y Electrónica e Informática Industrial, Universidad Politécnica de Madrid.
Un variador de frecuencia (VFD, por sus siglas en inglés) es un dispositivo esencial en la electrónica de potencia, utilizado para controlar la velocidad de los motores eléctricos al ajustar la frecuencia de la corriente que se les suministra. Además de su función básica, los variadores de frecuencia pueden operar en diferentes modos dependiendo de la aplicación específica. En este artículo, exploraremos tres modos de operación de los variadores de frecuencia: modo generador, modo convertidor de red y modo marino o aislado, basándonos en manuales de aplicación para proporcionar una visión clara de su funcionamiento y beneficios.
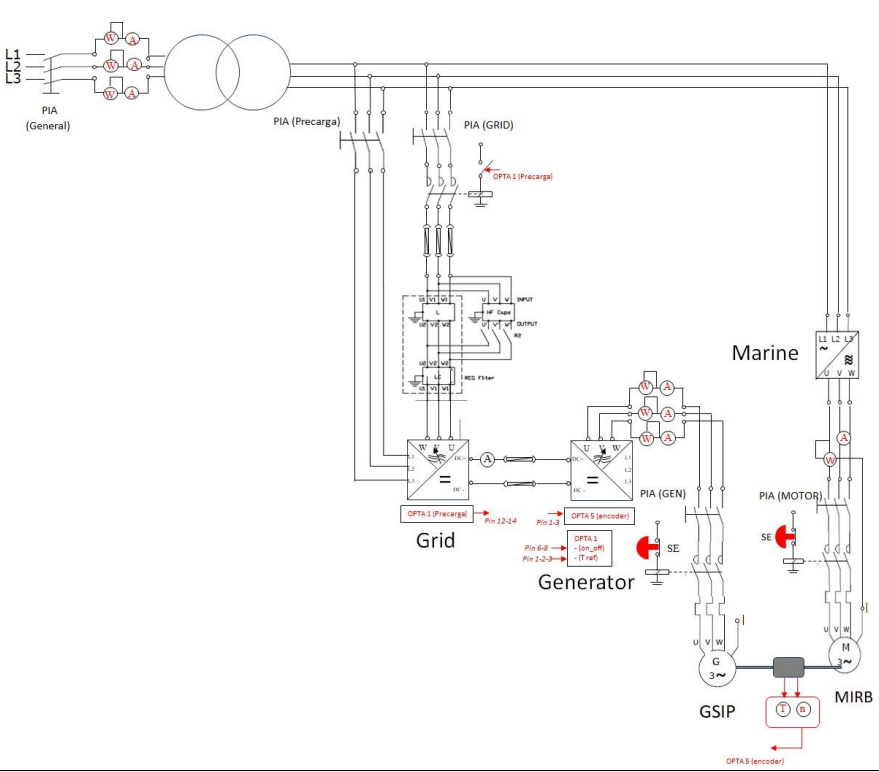
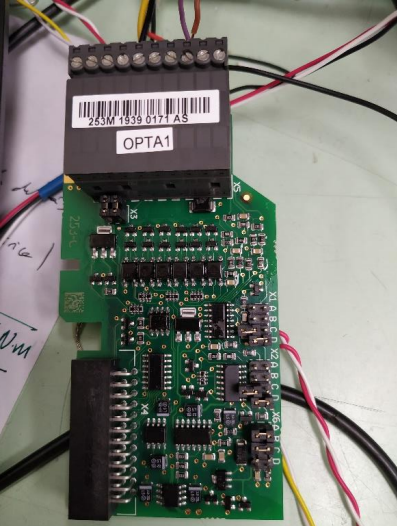
Modo generador: producción de energía
El modo generador de un variador de frecuencia está diseñado para aplicaciones de generación eléctrica. Este modo es comúnmente utilizado en sistemas de generación de energía eólicos o hidroeléctricos, donde el generador convierte la energía mecánica en energía eléctrica.
En este modo, el variador de frecuencia actúa como un convertidor de energía, permitiendo que la energía generada por el motor sea inyectada a la red eléctrica o almacenada para su uso posterior. El manual VACON ARFIFF30 describe cómo un variador de frecuencia operando en modo generador regula la frecuencia y la tensión de salida, asegurando que la electricidad generada sea compatible con las necesidades de la red eléctrica.
El modo generador ofrece varios beneficios clave. Permite la recuperación de energía en sistemas donde el motor actúa como generador, lo que optimiza la eficiencia energética al aprovechar la energía mecánica para inyectarla nuevamente a la red. Este modo es especialmente importante en aplicaciones de energía renovable, como en las turbinas eólicas, donde el generador convierte el movimiento mecánico en electricidad, contribuyendo así a la producción de energía limpia y sostenible.
Modo convertidor de red: integración con la red eléctrica
El modo convertidor de red permite que el variador de frecuencia funcione como un puente de conexión entre un sistema de generación de energía (como una planta de energía renovable) y la red eléctrica. Este modo es especialmente relevante cuando se requiere controlar y adaptar la energía generada para que sea compatible con las normas de calidad de la red, como las especificaciones de frecuencia, tensión y factor de potencia.
En el manual VACON ARFIF106 se detalla cómo el variador de frecuencia, en este modo, actúa como un convertidor bidireccional, gestionando la potencia tanto en la entrada (de la red hacia el sistema) como en la salida (desde el sistema hacia la red). Este tipo de operación es crucial en la generación distribuida, donde las fuentes de energía renovables se conectan a la red eléctrica, garantizando que la energía inyectada cumpla con los códigos de red establecidos, que incluyen limitaciones de frecuencia, armónicos y fluctuaciones de tensión.
El modo convertidor de red ofrece importantes beneficios, entre los que destaca su capacidad para interconectar sistemas de energía renovable con la red pública de manera eficiente. Este modo asegura que la energía inyectada cumpla con los estrictos códigos de calidad de la red, garantizando una integración sin problemas. Además, es esencial en la gestión de energía distribuida, como en instalaciones solares o eólicas, que requieren sincronización con la red para garantizar un suministro estable y controlado.
Modo marino o aislado: operación autónoma
El modo marino o aislado es específico para aplicaciones donde el variador de frecuencia debe operar independientemente de la red eléctrica, como en plataformas marinas o barcos. En este modo, el variador de frecuencia no depende de una conexión externa a la red para operar y, por lo tanto, debe manejar de forma autónoma la generación de energía y el suministro de energía al sistema sin la necesidad de sincronización con la red.
Según el manual VACON APFIFF09, este modo es utilizado en aplicaciones donde las condiciones ambientales requieren una operación fiable y estable sin conexión constante a una red. En estos sistemas, el variador ajusta la frecuencia y la tensión de salida para que coincidan con las necesidades de los motores o sistemas de propulsión sin necesidad de intervención externa.
El modo marino o aislado ofrece varios beneficios clave. Permite que el sistema funcione de manera autónoma, lo cual es esencial en aplicaciones fuera de la red, como barcos y plataformas offshore. Este modo asegura la estabilidad y confiabilidad del suministro energético en lugares remotos o aislados, donde el acceso a fuentes de energía externas es limitado o inexistente. Además, facilita el control de la velocidad de los motores y sistemas, sin necesidad de depender de fuentes externas de energía, lo que lo convierte en una opción ideal para entornos autónomos.
En conclusión, los variadores de frecuencia son dispositivos esenciales en una amplia variedad de aplicaciones, desde la generación de energía hasta el control de motores en sistemas aislados. A través de sus diferentes modos de operación, como modo generador, modo convertidor de red y modo marino o aislado, los variadores de frecuencia ofrecen flexibilidad, eficiencia y control preciso sobre la energía eléctrica. Estos dispositivos, al ser configurables para distintas aplicaciones, son fundamentales para optimizar el rendimiento y la eficiencia energética en sectores tan diversos como la energía renovable, la industria marina, y la gestión de redes eléctricas. Sin duda, los variadores de frecuencia son una pieza clave en la electrónica de potencia moderna.
La electrónica de potencia en 5 minutos
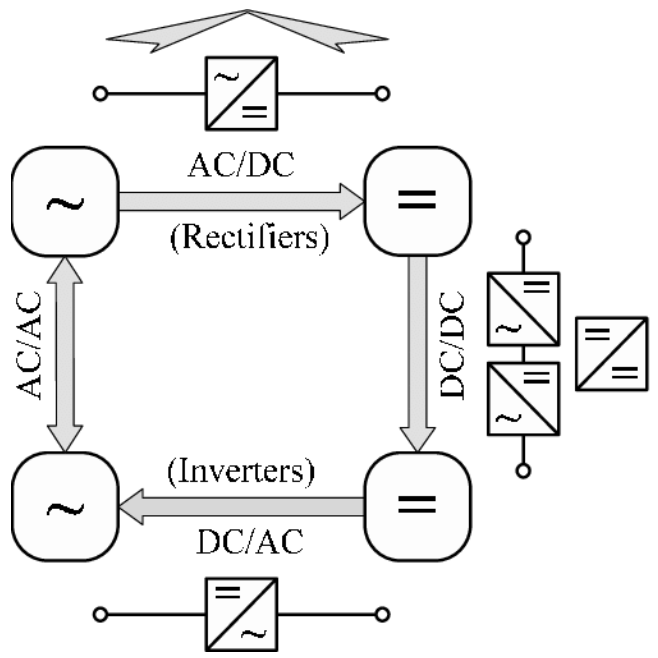
Autor:
Kumar V. Mahtani Mahtani
Profesor Ayudante Doctor en el Departamento de Automática, Ingeniería Eléctrica y Electrónica e Informática Industrial, Universidad Politécnica de Madrid.
La electrónica de potencia se centra en la conversión, control y distribución eficiente de energía eléctrica mediante dispositivos semiconductores. Es esencial en sistemas como fuentes de alimentación, accionamientos de motores y transmisión de energía. Este campo abarca varias técnicas y dispositivos de conversión, y en este artículo repasamos las principales configuraciones de conversión de energía: CA a CC, CA a CA, CC a CC, y CC a CA.
Conversión CA-CC
La conversión de corriente alterna (CA) a corriente continua (CC) se realiza a través de los rectificadores. Estos circuitos se utilizan para transformar la corriente alterna que proviene de la red eléctrica en corriente continua, y son fundamentales en muchas aplicaciones de electrónica de potencia. Los rectificadores se pueden clasificar según el tipo de fuente de CA (monofásica o trifásica) y el tipo de interruptor semiconductor utilizado. Los principales dispositivos en estos rectificadores son los diodos (dispositivos no controlados) y los tiristores o SCR (dispositivos controlados).
Los rectificadores se utilizan ampliamente en aplicaciones de electrónica de potencia, como los accionamientos de motores de CA y CC, y en sistemas de transmisión de CC de alta tensión (HVDC). En las aplicaciones más simples, se usan rectificadores de diodo, que no permiten controlar la salida de la corriente continua. Sin embargo, en situaciones donde se necesita un control de la tensión de salida CC, como en los accionamientos de motores de CA y CC, se emplean tiristores para controlar la fase de la frecuencia de la red eléctrica.
Además, el uso de rectificadores en los sistemas de potencia debe ser cuidadosamente gestionado, ya que si no se aplican correctamente, pueden generar armónicos y reducir el factor de potencia, afectando negativamente a la red eléctrica. Esto se debe a las fluctuaciones en la corriente que se producen cuando los rectificadores operan con una señal no ideal de CA.
Conversión CA-CA
La conversión de CA a CA es más compleja, ya que involucra la variación tanto de la tensión como de la frecuencia. Para realizar este tipo de conversión, se utilizan circuitos como los controladores de CA y los cicloconvertidores.
1. Controladores de CA: Estos convertidores permiten transformar una tensión fija de frecuencia fija en una tensión variable con frecuencia fija. Son típicamente utilizados en aplicaciones como controladores de motores monofásicos y atenuadores de luz. En estos casos, la frecuencia de salida se mantiene constante, pero la tensión puede ajustarse según sea necesario.
2. Cicloconvertidores: Estos dispositivos permiten una conversión más compleja, transformando una tensión fija de frecuencia fija en una tensión variable con frecuencia variable. Son especialmente utilizados en aplicaciones de alta potencia, como los motores de inducción y motores síncronos, que requieren un control preciso de la frecuencia y fase de la CA. Los tiristores se utilizan en estos sistemas debido a su capacidad para conmutar la fase de manera eficiente.
El control de CA se realiza principalmente mediante el uso de tiristores, que permiten regular parámetros como la temperatura, la iluminación y el control de motores de inducción. Los métodos más comunes de control incluyen:
- Control de fase, que ajusta la fase de la corriente.
- Control de encendido y apagado, que controla cuándo se enciende y apaga el dispositivo.
- Control de tiempo proporcional, que ajusta la duración de las fases de operación según las necesidades de la carga.
Conversión CC-CC
La conversión de CC a CC se realiza a través de los choppers o convertidores de conmutación. Estos dispositivos permiten aumentar o disminuir el nivel de tensión de una fuente de corriente continua (como una batería, celda solar o pila de combustible) a otro nivel de corriente continua. Esta conversión es clave en aplicaciones como la transmisión de CC de alta tensión y en la alimentación de dispositivos de baja potencia.
Los choppers son esenciales en los sistemas de transmisión HVDC, ya que permiten la conversión eficiente de energía eléctrica a través de largas distancias. Los dispositivos más utilizados en estos choppers incluyen IGBTs y MOSFETs para aplicaciones de baja potencia, y SCRs o tiristores para aplicaciones de alta potencia.
Existen dos tipos principales de choppers:
- Chopper reductor o convertidor Buck: Reduce la tensión de entrada.
- Chopper elevador o convertidor Boost: Aumenta la tensión de entrada.
Además, se utilizan fuentes de alimentación con conmutador, que emplean un regulador de conmutación para mejorar la eficiencia en la conversión de la energía, disipando menos calor que los reguladores lineales tradicionales.
Los convertidores CC-CC se utilizan principalmente en aplicaciones como las fuentes de alimentación de CC y en convertidores de frecuencia para motores de CC. A menudo, la entrada a estos convertidores es una tensión no regulada de CC, que se obtiene al rectificar la tensión de la red de CA. Como resultado, la tensión de entrada puede fluctuar dependiendo de las variaciones en la amplitud de la tensión de la red eléctrica. El convertidor CC-CC proporciona una salida controlada de CC en el nivel de tensión deseado.
Conversión CC-CA
La conversión de CC a CA se realiza mediante inversores, que convierten una fuente de CC en una tensión sinusoidal de CA. Este tipo de conversión es esencial para aplicaciones como la alimentación de cargas de CA, el control de motores de CA, o la interconexión de dispositivos de CC con la red eléctrica.
Los inversores se clasifican según su salida de CA en monofásicos y trifásicos, y pueden ser de puente medio o puente completo. Un inversor comúnmente se utiliza en sistemas de fuentes de alimentación ininterrumpida (SAI), donde se necesita una salida de CA sinusoidal con frecuencia y amplitud controladas.
Para los convertidores de frecuencia, dado que es difícil cambiar directamente la frecuencia de la onda CA, la conversión inicial consiste en transformar la CA en CC, lo cual es relativamente sencillo. Una vez que se tiene la tensión continua, es más fácil manipularla para obtener una frecuencia de salida específica. Los convertidores de frecuencia incluyen tres componentes esenciales:
- Rectificador: Convierte la CA en CC.
- Bus de CC: Almacena la energía en forma de corriente continua.
- Inversor: Convierte la energía almacenada en CC de vuelta a CA.
Los convertidores de frecuencia son fundamentales en aplicaciones como los accionamientos de motores de CA y en sistemas de alimentación ininterrumpida.
Conclusión
La electrónica de potencia es un campo clave en la gestión eficiente de la energía eléctrica, abarcando tecnologías de conversión que permiten transformar, controlar y distribuir la energía de manera efectiva. Ya sea en la conversión de CA a CC, CA a CA, CC a CC, o CC a CA, los dispositivos semiconductores, como los diodos, tiristores, IGBTs y MOSFETs, son fundamentales en el control y manipulación de la energía eléctrica. La correcta implementación de estos sistemas permite un uso más eficiente de la energía, mejora la calidad de la energía en la red eléctrica y optimiza el rendimiento de una amplia gama de aplicaciones, desde motores eléctricos hasta transmisión de energía de largo alcance.
“Cultura” de laboratorio: sobre osciloscopios y sondas
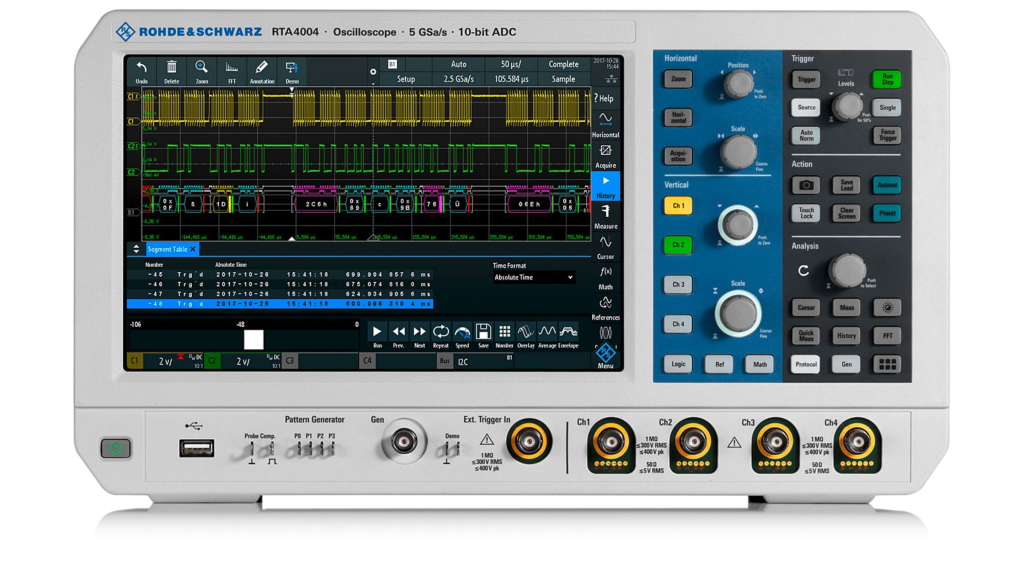
Autor:
Kumar V. Mahtani Mahtani
Profesor Ayudante en el Departamento de Automática, Ingeniería Eléctrica y Electrónica e Informática Industrial, Universidad Politécnica de Madrid.
Artículo realizado a partir de la información de la empresa Rohde&Schwarz. Todas las figuras son propiedad de dicha empresa.
El osciloscopio es una herramienta esencial en la electrónica, utilizada para visualizar y analizar señales eléctricas. Pero, para obtener mediciones precisas y fiables, es necesario comprender no solo el funcionamiento básico del osciloscopio, sino también cómo interactuar con las sondas que se utilizan para capturar las señales. Las sondas son piezas clave en la medición, ya que conectan el osciloscopio con el circuito en el que se mide la señal. Existen diferentes tipos de sondas, cada una adecuada para diferentes aplicaciones y situaciones, y es fundamental entender cómo utilizarlas correctamente para obtener resultados precisos.
Tipos de sondas: pasivas vs. activas
Existen dos tipos principales de sondas para osciloscopios: las pasivas y las activas. Cada una tiene sus propias ventajas y limitaciones, y la elección entre una u otra depende de la aplicación específica. Las sondas pasivas son las más sencillas y económicas. No requieren una fuente de energía externa, lo que las hace muy prácticas y fáciles de usar. Estas sondas son ideales para tareas generales y se incluyen comúnmente con los osciloscopios. Se caracterizan por su robustez y fiabilidad, y son especialmente útiles para medir señales en una amplia gama de frecuencias sin complicaciones.
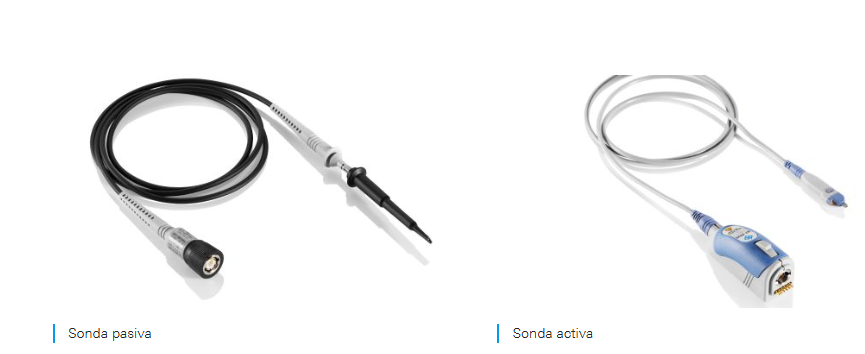
Por otro lado, las sondas activas son más sofisticadas y costosas. Estas sondas incluyen componentes activos, como transistores de efecto de campo (FET), que permiten manejar señales de alta frecuencia con mayor precisión. Las sondas activas ofrecen un rendimiento superior en términos de ancho de banda y precisión, lo que las hace imprescindibles en aplicaciones que requieren medidas detalladas de señales rápidas y de alta frecuencia, como las utilizadas en circuitos de RF o comunicaciones. Aunque su precio es más elevado, su capacidad para ofrecer una medición más precisa justifica la inversión en situaciones de alta demanda.
Compensación de las sondas pasivas
Una de las prácticas más importantes al usar sondas pasivas es la compensación. Si no se realiza la compensación correctamente, la señal medida puede aparecer distorsionada, especialmente a altas frecuencias, lo que afecta la precisión de los resultados. La compensación ajusta la capacidad eléctrica de la sonda para que la forma de onda que se mide sea lo más fiel posible a la señal original.

El proceso de compensación de una sonda pasiva es sencillo pero crucial. Primero, se conecta la sonda al osciloscopio y se coloca el cable de puesta a tierra. Luego, se utiliza una señal de referencia, como una onda cuadrada de 1000 Hz, que la mayoría de los osciloscopios incorporan para facilitar este proceso. Ajustando el condensador de compensación en la sonda hasta que la forma de onda cuadrada se vea lo más rectangular posible, se logra la compensación adecuada. Si la forma de onda tiene picos en los flancos, se sabe que la sonda está sobrecompensada o infracompensada, lo que se corrige ajustando el condensador de forma precisa.
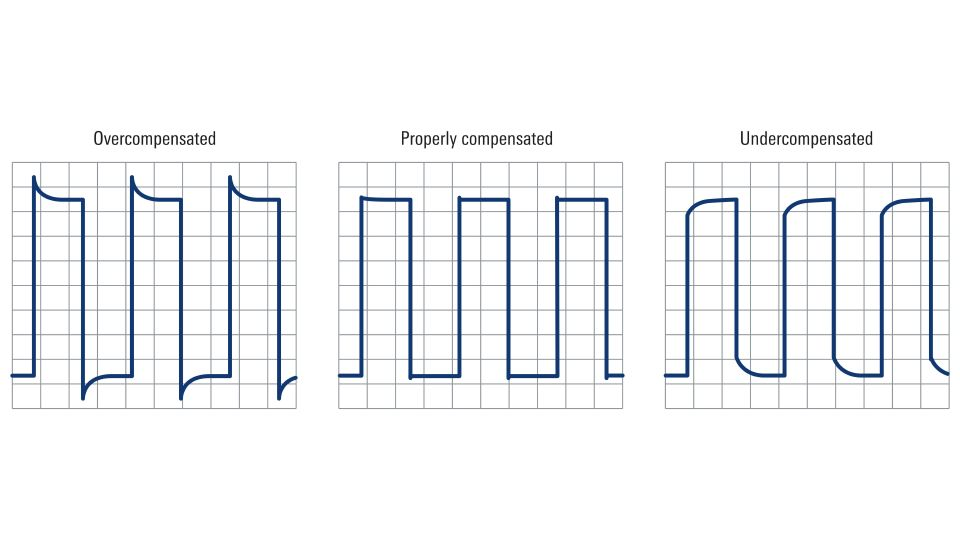
Cables de puesta a tierra cortos para una mejor precisión
Otro consejo clave es utilizar cables de puesta a tierra lo más cortos posible. Las sondas pasivas miden la señal en relación con la masa, y una conexión a tierra adecuada es esencial para obtener mediciones correctas. Sin embargo, los cables de puesta a tierra largos pueden introducir inductancia adicional, lo que afecta negativamente las señales, especialmente a frecuencias altas. Esto puede generar sobreoscilaciones, distorsiones o errores en las mediciones. Por lo tanto, siempre que sea posible, se deben usar cables cortos y de buena calidad para reducir estos efectos indeseados.
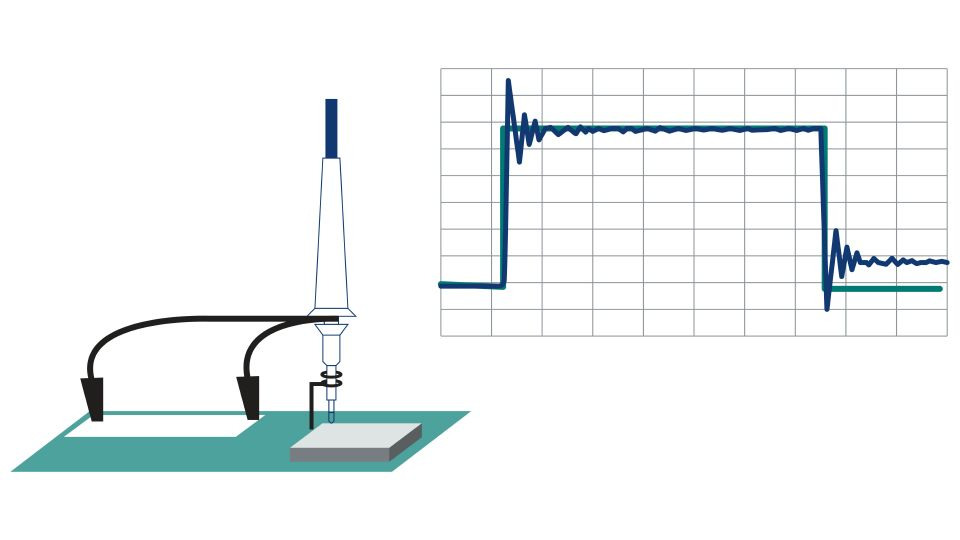
Impedancia de entrada correcta: la clave para medidas fiables
La impedancia de entrada es otro factor crucial en el proceso de medición con osciloscopios. Algunos osciloscopios permiten seleccionar entre diferentes impedancias de entrada, típicamente 50 ohmios o 1 megaohmio. La selección correcta depende de la naturaleza de la señal que se está midiendo. Por ejemplo, para señales de alta frecuencia o RF, es común utilizar una impedancia de entrada de 50 ohmios, mientras que las sondas pasivas generalmente funcionan mejor con una impedancia de 1 megaohmio.
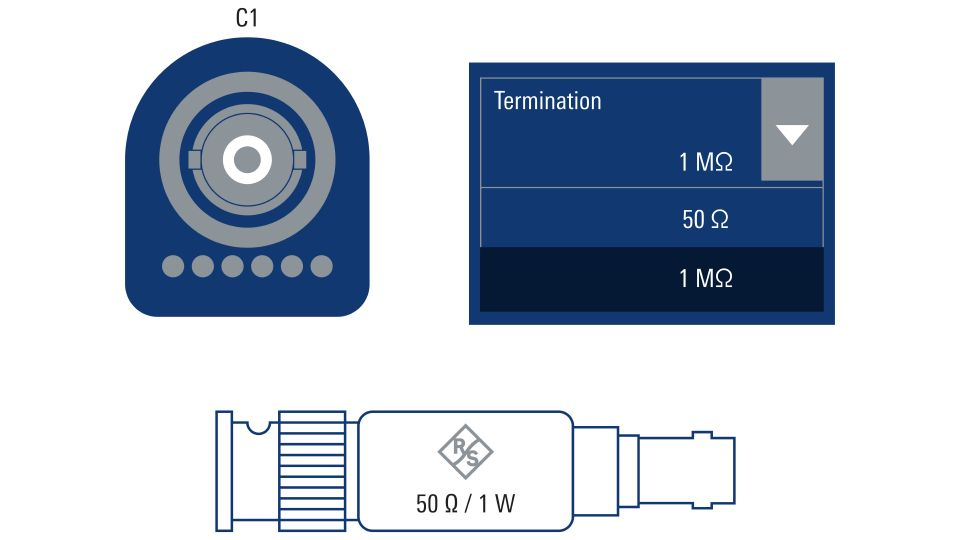
Elegir la impedancia correcta asegura que las mediciones sean precisas. Si se selecciona una impedancia incorrecta, la señal medida puede ser incorrecta. En aplicaciones de alta frecuencia, como en pruebas de RF, es vital elegir la impedancia adecuada para evitar distorsiones en las señales y asegurar la exactitud de las mediciones.
Sondas de corriente y la función de desmagnetización
Las sondas de corriente, que se utilizan para medir la corriente en un circuito, tienen una particularidad que puede afectar la precisión de las mediciones: el fenómeno de retención del magnetismo. Después de medir una corriente, especialmente en circuitos que se encienden y apagan, la sonda puede retener una cierta cantidad de magnetismo, lo que introduce un “offset” o desviación en las mediciones posteriores. Para resolver este problema, muchas sondas de corriente cuentan con una función de desmagnetización, que se activa para eliminar el magnetismo residual.
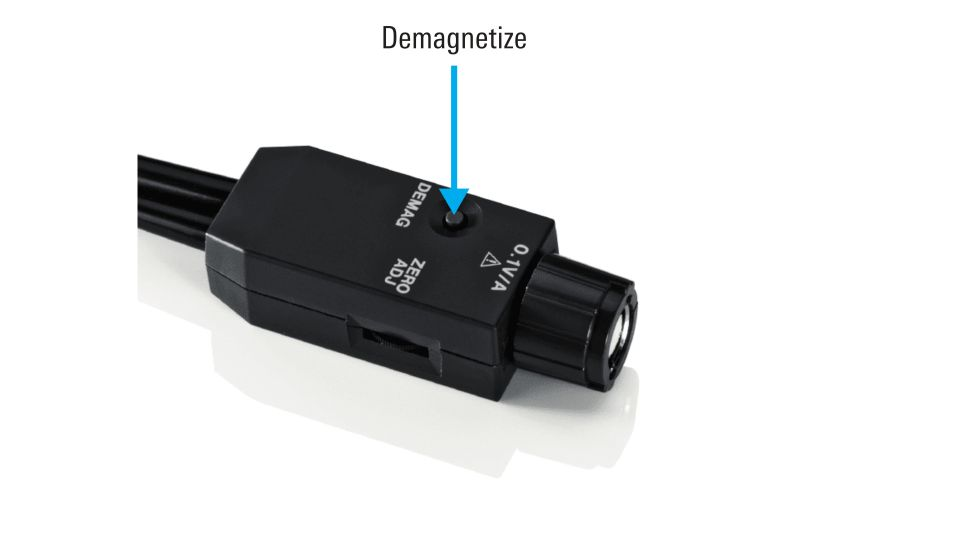
El proceso de desmagnetización es rápido y eficaz, y se debe realizar antes de cada medición para asegurar que las lecturas sean precisas. Al activar la función de desmagnetización, la sonda genera una señal especial que elimina cualquier magnetismo residual y restablece la sonda a su estado inicial, listo para una medición precisa.
Mejora de sensibilidad con devanados adicionales
Una forma sencilla de mejorar la sensibilidad de las sondas de corriente es arrollar el conductor a través de la sonda varias veces. Al hacerlo, se aumenta la sensibilidad de la medición de manera lineal con el número de vueltas del conductor. Por ejemplo, si el conductor pasa por la sonda 4 veces, la sensibilidad aumenta en un factor de 4. Este método es particularmente útil cuando se miden corrientes pequeñas. Aunque el número de arrollamientos incrementa la impedancia de inserción, este efecto es mínimo y no suele afectar la precisión de las mediciones.
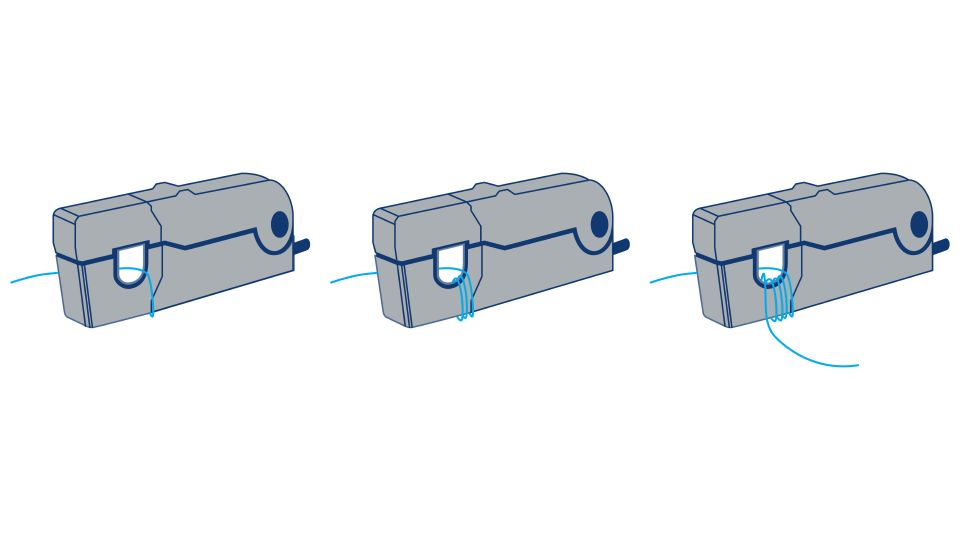
Sondas diferenciales para medidas flotantes
En ocasiones, es necesario realizar mediciones en puntos del circuito que no están conectados a tierra, lo que se conoce como medición flotante. Para estas mediciones, las sondas diferenciales son la herramienta ideal. A diferencia de las sondas convencionales, que miden la tensión con respecto a tierra, las sondas diferenciales miden la diferencia de tensión entre dos puntos de un circuito, lo que las hace perfectas para señales flotantes.
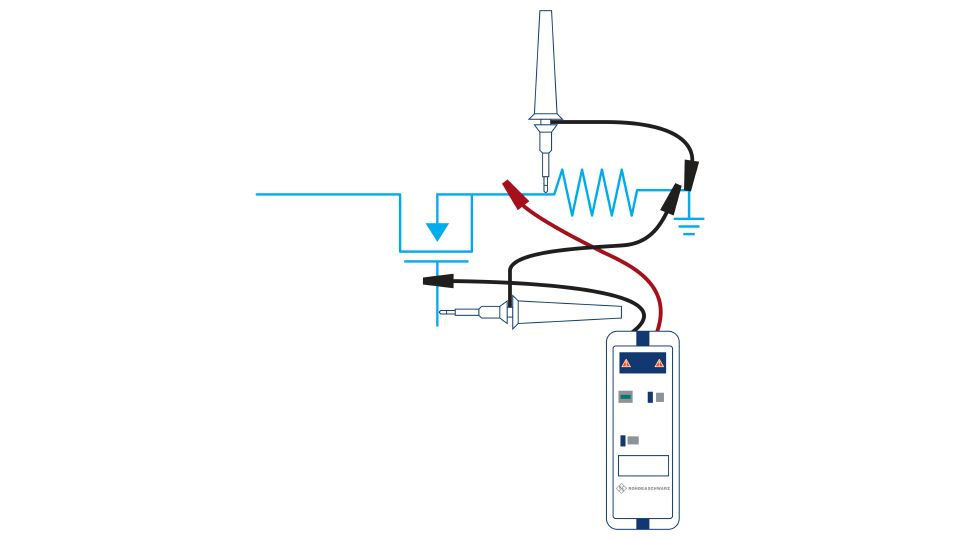
Las sondas diferenciales tienen la ventaja de ofrecer una mayor precisión al rechazar el ruido en modo común, es decir, el ruido que afecta a ambas entradas de manera similar. Esto las hace esenciales en entornos donde las señales flotantes deben medirse con alta precisión y sin interferencias. Además, las sondas diferenciales protegen tanto a los equipos como a los operadores de los riesgos asociados con las conexiones a tierra accidentales.
Sondas activas para medidas de alta precisión
Para las aplicaciones más exigentes, como la medición de señales de alta frecuencia o señales de baja amplitud superpuestas a señales de alta intensidad, las sondas activas son la mejor opción. Estas sondas ofrecen una capacitancia de entrada significativamente menor en comparación con las sondas pasivas, lo que reduce la carga en el circuito y permite una reproducción más precisa de la señal medida. Además, su mayor ancho de banda las hace ideales para señales rápidas, como las de las fuentes de alimentación con rizado.
En resumen, el uso correcto de las sondas con osciloscopios es esencial para obtener mediciones precisas y fiables. La elección entre sondas pasivas y activas, la correcta compensación de las sondas pasivas, el uso adecuado de los cables de tierra y la selección de la impedancia de entrada correcta son solo algunas de las prácticas que garantizan mediciones precisas. Con una comprensión adecuada de cómo utilizar estas herramientas y un enfoque cuidadoso en las mediciones, los estudiantes de electrónica podrán aprovechar al máximo las capacidades de sus osciloscopios y obtener resultados más fiables y detallados.
STATCOM y SVC: Soluciones para la gestión de la potencia reactiva en redes eléctricas
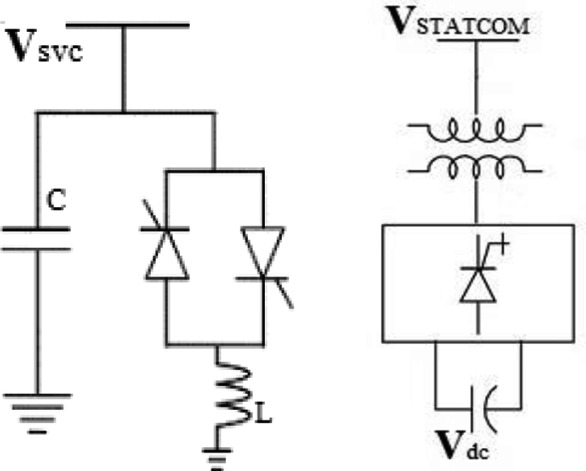
Autor:
Kumar V. Mahtani Mahtani
Profesor Ayudante en el Departamento de Automática, Ingeniería Eléctrica y Electrónica e Informática Industrial, Universidad Politécnica de Madrid.
En el complejo y dinámico mundo de la calidad de la energía eléctrica, la gestión eficiente de la potencia reactiva juega un papel crucial para mantener la estabilidad y la eficiencia de los sistemas de transmisión y distribución. La potencia reactiva es fundamental en el funcionamiento de las redes eléctricas, ya que contribuye a crear el campo magnético necesario para el funcionamiento de motores y transformadores. Sin embargo, cuando la cantidad de potencia reactiva es inadecuada, puede provocar fluctuaciones en la tensión y afectar la calidad de la energía. Aquí es donde tecnologías como el STATCOM (Compensador Síncrono Estático) y el SVC (Compensador Estático de VAR) entran en juego, cada una con características y aplicaciones particulares que las hacen más o menos adecuadas según las necesidades del sistema.
Potencia reactiva: el motor oculto de la red eléctrica
Para comprender cómo funcionan estas tecnologías, primero debemos entender el concepto de potencia reactiva. En un sistema eléctrico, la potencia activa es la que realmente realiza trabajo, como mover motores o alimentar dispositivos eléctricos. Por otro lado, la potencia reactiva no realiza trabajo directamente, pero es necesaria para crear los campos magnéticos que permiten el funcionamiento de equipos como motores, transformadores y generadores. La potencia reactiva, aunque no hace trabajo útil directamente, es esencial para el mantenimiento de la estabilidad del sistema de transmisión y distribución de energía.
Podemos pensar en la red eléctrica como un vehículo en movimiento. La potencia activa sería el motor que impulsa el vehículo, mientras que la potencia reactiva actuaría como el sistema de dirección y suspensión que mantiene el viaje estable y suave. Si hay demasiada potencia reactiva, el sistema puede volverse inestable, mientras que una falta de potencia reactiva puede dificultar el funcionamiento adecuado de la red. Los compensadores como el STATCOM y el SVC se encargan de gestionar esta potencia reactiva, inyectándola o absorbiéndola según sea necesario para mantener el equilibrio y la estabilidad de la red.
El SVC: El ajuste de suspensión para fluctuaciones moderadas
El Compensador Estático de VAR (SVC) es una tecnología más antigua que utiliza reactores controlados por tiristores y capacitores de derivación para inyectar o absorber potencia reactiva. Se puede imaginar al SVC como un sistema de suspensión de vehículo que se ajusta manualmente para mantener el confort del viaje. La principal ventaja del SVC es su capacidad para responder a fluctuaciones moderadas en la red eléctrica, como las que se producen en redes de transmisión de media distancia o en zonas industriales donde las cargas no cambian de forma rápida y radical.
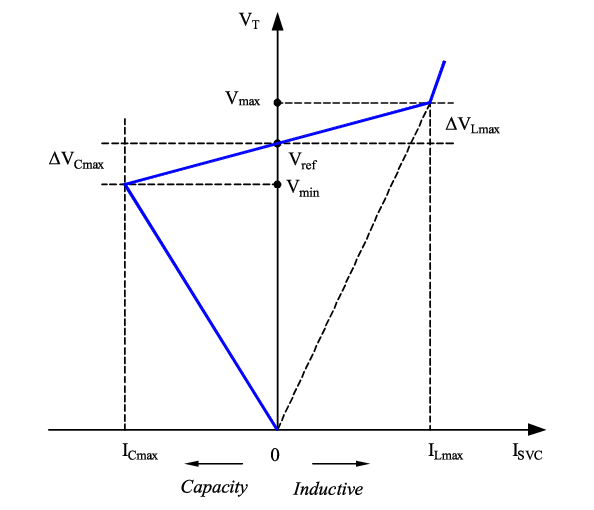
El SVC tiene un tiempo de respuesta en el rango de milisegundos, lo que lo hace ideal para situaciones en las que las variaciones de tensión no son excesivamente rápidas. El SVC se controla generalmente a través de señales de referencia de tensión, ajustando la potencia reactiva según las necesidades del sistema. Aunque es menos rápido que el STATCOM, el SVC sigue siendo muy efectivo en aplicaciones donde las fluctuaciones de tensión son más suaves y no se requiere una respuesta ultra rápida.
Además, el SVC es muy eficaz en redes donde la compensación de potencia reactiva es el principal objetivo, sin la necesidad de reducir las distorsiones armónicas o corregir desequilibrios de tensión que podrían ser necesarios en aplicaciones más dinámicas. En estos casos, el SVC se utiliza como una solución económica y eficiente para mantener la tensión dentro de los límites adecuados, asegurando la estabilidad del sistema sin requerir una tecnología demasiado avanzada.
El STATCOM: El cerebro electrónico para un control preciso
El Compensador Síncrono Estático (STATCOM) es una tecnología más avanzada que utiliza convertidores de fuente de tensión (VSC) para generar o absorber potencia reactiva. A diferencia del SVC, que emplea componentes pasivos como reactores y capacitores, el STATCOM emplea electrónica de potencia para ofrecer un control más preciso y flexible de la potencia reactiva. Esto le permite ajustar la respuesta mucho más rápidamente, lo que lo hace ideal para entornos donde las fluctuaciones de tensión son rápidas y de alta frecuencia.
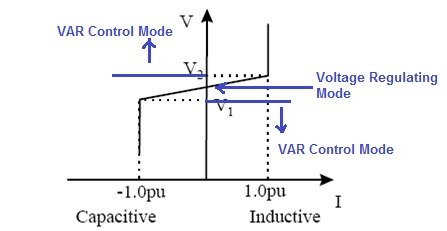
El STATCOM actúa como un sistema de dirección y suspensión avanzada para la red eléctrica, ajustando su respuesta en tiempo real a las fluctuaciones de tensión que se presentan en la red. El control digital avanzado, que se basa en algoritmos de control directo de corriente, permite que el STATCOM responda de manera extremadamente rápida a cambios en las condiciones de la red, lo que lo convierte en la opción preferida en situaciones donde la estabilidad de la red debe mantenerse bajo condiciones extremas o cuando se requiere un control de precisión más alto.
Con tiempos de respuesta que van desde los microsegundos hasta los milisegundos, el STATCOM es ideal para sistemas modernos que enfrentan fluctuaciones rápidas y dinámicas, como las que se encuentran en redes con alta penetración de fuentes de energía renovables o en aplicaciones industriales con cargas fluctuantes de alta velocidad. La flexibilidad del STATCOM también permite su instalación en contenedores, lo que facilita el transporte y la implementación en lugares remotos o con espacio limitado, lo que lo convierte en una solución versátil para una variedad de aplicaciones.
Comparación técnica y elección de la tecnología adecuada
A la hora de elegir entre el STATCOM y el SVC, es fundamental considerar las necesidades específicas de la red eléctrica y las condiciones de operación. El SVC es más adecuado para aplicaciones en las que se requiere una compensación de potencia reactiva a moderadas velocidades de respuesta. Por ejemplo, es ideal en redes de transmisión que experimentan fluctuaciones de tensión más lentas y donde no se requieren correcciones dinámicas rápidas. Además, el SVC es más sencillo y económico, lo que lo convierte en una opción atractiva para aplicaciones de menor complejidad.
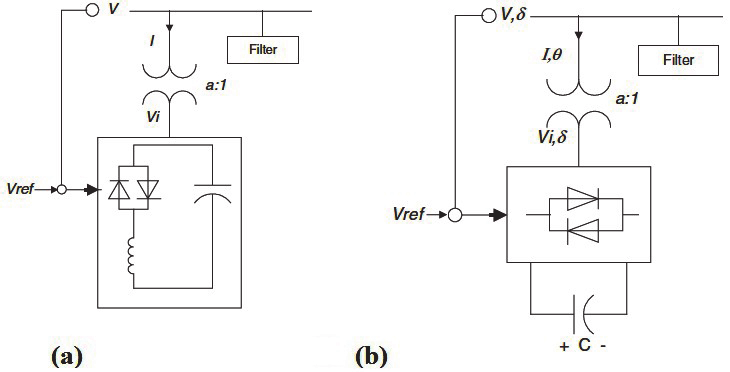
Por otro lado, el STATCOM es la mejor opción cuando se requieren tiempos de respuesta rápidos, especialmente en redes donde las fluctuaciones de tensión ocurren a alta velocidad o donde se necesita una corrección precisa de la potencia reactiva. Además, el STATCOM es más eficiente en la reducción de distorsiones armónicas y en la corrección de desequilibrios de tensión, lo que lo hace más adecuado para aplicaciones modernas, como las que involucran energías renovables intermitentes o sistemas con cargas industriales que cambian rápidamente.
Conclusión
En resumen, tanto el SVC como el STATCOM son tecnologías fundamentales para la gestión de la potencia reactiva y la estabilización de la red eléctrica. Mientras que el SVC es ideal para aplicaciones de compensación de potencia reactiva a velocidades moderadas y con un control relativamente simple, el STATCOM ofrece una solución más avanzada y precisa para sistemas que requieren respuestas rápidas y flexibles. La elección entre uno u otro dependerá de las características específicas de la red, las necesidades de compensación de potencia reactiva y la rapidez con la que se necesite ajustar la potencia para mantener la estabilidad y eficiencia del sistema. Ambas tecnologías continúan evolucionando, y su implementación será clave para afrontar los desafíos de la transmisión y distribución de energía en un mundo cada vez más interconectado y dependiente de fuentes de energía renovables.
HVDC, el juego de las grandes distancias
Autor:
Kumar V. Mahtani Mahtani
Profesor Ayudante en el Departamento de Automática, Ingeniería Eléctrica y Electrónica e Informática Industrial, Universidad Politécnica de Madrid.
La transmisión en corriente continua de alta tensión (HVDC, por sus siglas en inglés) ha revolucionado el transporte de energía eléctrica a largas distancias. Esta tecnología ofrece una serie de ventajas sobre la transmisión en corriente alterna (HVAC), especialmente cuando se trata de distancias largas o de la interconexión de redes de distintas frecuencias. En este artículo, exploraremos cómo funciona la transmisión HVDC, sus principales ventajas y desventajas, los tipos de enlaces utilizados y algunos detalles técnicos sobre los convertidores involucrados.

¿Cómo funciona el sistema HVDC?
El sistema HVDC convierte la energía de corriente alterna (CA), generada en las plantas eléctricas, en corriente continua (CC) para su transporte a largas distancias, y luego reconvierte esta corriente continua nuevamente a corriente alterna en el extremo receptor para ser distribuida en la red. Este proceso de conversión se realiza mediante el uso de rectificadores y convertidores.
1. Conversión de CA a CC: En el extremo de generación, la energía en corriente alterna pasa por un rectificador, un dispositivo que convierte la corriente alterna en corriente continua. Los rectificadores son componentes clave en el sistema HVDC, y su función es asegurar una conversión eficiente de la energía para su transporte a largas distancias.
2. Transporte de Energía en CC: Una vez convertida en corriente continua, la energía viaja a través de las líneas de transmisión HVDC. Esta forma de transmisión tiene la ventaja de reducir las pérdidas de energía, ya que la corriente continua no sufre los efectos de la resistencia del conductor de la misma manera que la corriente alterna.
3. Conversión de CC a CA: En el extremo receptor, la corriente continua pasa por un inversor, que convierte la corriente continua nuevamente en corriente alterna para su distribución en la red eléctrica. Los inversores son esenciales para devolver la energía a la forma en que los sistemas de distribución de energía la utilizan comúnmente.
El sistema de conversión a través de rectificadores e inversores es clave para la efectividad del sistema HVDC. Estos dispositivos, aunque costosos, permiten una transmisión más eficiente, especialmente en líneas largas.
Ventajas de la transmisión HVDC
La tecnología HVDC tiene varias ventajas notables sobre la transmisión en corriente alterna, particularmente en distancias largas o cuando se interconectan redes con diferentes frecuencias:
Menores pérdidas de energía: La transmisión en corriente continua presenta menos pérdidas de energía en comparación con la corriente alterna, lo que la hace más eficiente, especialmente a distancias superiores a los 600 km en líneas aéreas o 50 km en cables subterráneos.
Reducción de costes en infraestructura: Aunque el coste inicial de los sistemas HVDC es alto debido a los equipos de conversión, el coste de las líneas de transmisión en sí mismas es más bajo en comparación con las líneas de corriente alterna. Además, se requieren menos conductores y aisladores, lo que reduce los costes operativos.
Interconexión de redes con diferentes frecuencias: Un aspecto importante de HVDC es su capacidad para interconectar redes que operan a diferentes frecuencias, sin que haya necesidad de sincronizar las frecuencias de ambas redes. Esto permite la conexión de redes que, de otra manera, no podrían compartir energía.
No hay pérdidas por efecto piel o proximidad: A diferencia de los sistemas HVAC, que experimentan pérdidas de energía debido al efecto piel (la tendencia de las corrientes alternas a concentrarse en la superficie de los conductores) y el efecto de proximidad (la influencia de la corriente en los conductores cercanos), los sistemas HVDC no están sujetos a estos fenómenos, lo que mejora la eficiencia en la transmisión.
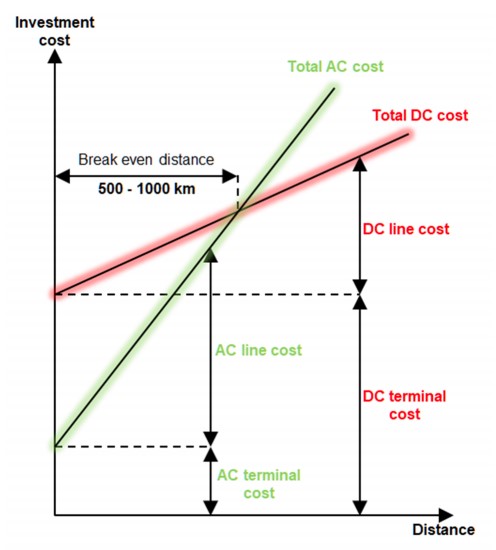
Inconvenientes de la transmisión HVDC
A pesar de sus ventajas, la transmisión HVDC también presenta algunas desventajas:
Coste inicial alto: La principal desventaja de los sistemas HVDC es el alto coste inicial de las estaciones convertidoras (rectificadores e inversores), que son mucho más caros que los transformadores empleados en los sistemas HVAC.
Generación de armónicos: Los rectificadores y los inversores generan armónicos, que son distorsiones de la señal eléctrica que pueden afectar a otros equipos y sistemas conectados a la red. Para minimizar estos efectos, es necesario emplear filtros activos, lo que añade más costes al sistema.
Fallos en subestaciones de CA: Si ocurre una falla en la subestación de corriente alterna (por ejemplo, en el extremo de recepción), esto puede causar una interrupción en la transmisión de energía en el sistema HVDC. Esta dependencia de la subestación HVAC puede ser un inconveniente en situaciones de emergencia.
Tipos de enlaces HVDC
Existen varios tipos de enlaces HVDC, que se utilizan según las necesidades específicas del proyecto de transmisión:
Enlace monopolar: Este tipo de enlace utiliza un solo conductor de polaridad negativa y una ruta de retorno que generalmente es la tierra o el mar. Aunque es más económico, el enlace monopolar tiene limitaciones importantes, como el riesgo asociado con el uso de la tierra como retorno.

Enlace bipolar: El enlace bipolar utiliza dos conductores, uno positivo y otro negativo, con un sistema de retorno a tierra. Este tipo de enlace es más robusto, ya que si uno de los conductores falla, el sistema puede operar en modo monopolar, lo que garantiza que la transmisión de energía continúe. Es el tipo de enlace más común en los sistemas HVDC modernos.

Enlace homopolar: En este enlace, ambos conductores tienen la misma polaridad (generalmente negativa), y utilizan un sistema de retorno a tierra o metálico. Aunque es más económico, no se utiliza mucho hoy en día debido a problemas de estabilidad y eficiencia.

Convertidores en los sistemas HVDC
El núcleo de un sistema HVDC es el proceso de conversión de energía entre corriente alterna y corriente continua, que se lleva a cabo mediante rectificadores e inversores. Los rectificadores convierten la energía de corriente alterna a corriente continua, mientras que los inversores realizan el proceso inverso.
Rectificadores: Se utilizan principalmente en el extremo de generación de energía para convertir la corriente alterna a corriente continua. Los rectificadores más comunes en sistemas HVDC son los de electrónica de potencia, como los rectificadores de tiristores. Estos dispositivos permiten una conversión eficiente, pero generan armónicos que deben ser controlados mediante filtros.
Inversores: Al final de la línea de transmisión, los inversores convierten la corriente continua nuevamente a corriente alterna. Estos dispositivos son esenciales para asegurar que la energía transmitida a través de las líneas HVDC pueda ser utilizada por los sistemas de distribución convencionales. Al igual que los rectificadores, los inversores también generan armónicos que deben ser mitigados.
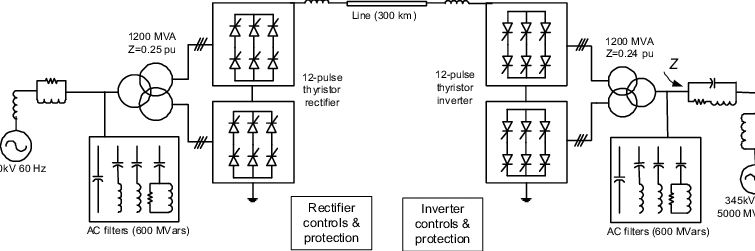
Los convertidores de tiristores son cruciales en este proceso, ya que permiten una regulación precisa del flujo de energía. Sin embargo, los sistemas más avanzados también emplean convertidores de IGBT (transistores bipolares de puerta aislada), que ofrecen un control más preciso y una mayor capacidad de sobrecarga, lo que mejora la eficiencia general del sistema.
Ejemplos de proyectos HVDC
Algunos ejemplos destacados de proyectos de transmisión HVDC incluyen:
- Xiangjiaba-Shanghai en China, que transporta 6.400 MW a través de una distancia de 2.071 km.
- Murraylink en Australia, un sistema de transmisión subterránea de 180 km.
- NorNed entre Noruega y los Países Bajos, con una interconexión de 580 km.
- NordE.ON 1 en el Mar del Norte, conectando plataformas marítimas con la tierra firme.
Estos proyectos muestran cómo la tecnología HVDC ha sido fundamental para mejorar la transmisión de energía, conectar redes eléctricas distantes y asegurar un suministro estable de energía en diferentes regiones del mundo.
Conclusión
La transmisión HVDC ofrece una serie de ventajas significativas, especialmente en la transmisión de energía a largas distancias. Aunque el coste inicial y los equipos involucrados pueden ser elevados, la reducción de las pérdidas de energía, la posibilidad de interconectar redes de diferentes frecuencias y la mayor eficiencia hacen de esta tecnología una opción cada vez más atractiva. Con el continuo avance de los convertidores y otros equipos electrónicos de potencia, es probable que la transmisión HVDC juegue un papel cada vez más importante en el futuro de la infraestructura energética global.
Suministro de energía eléctrica a electrolizadores: topologías más empleadas
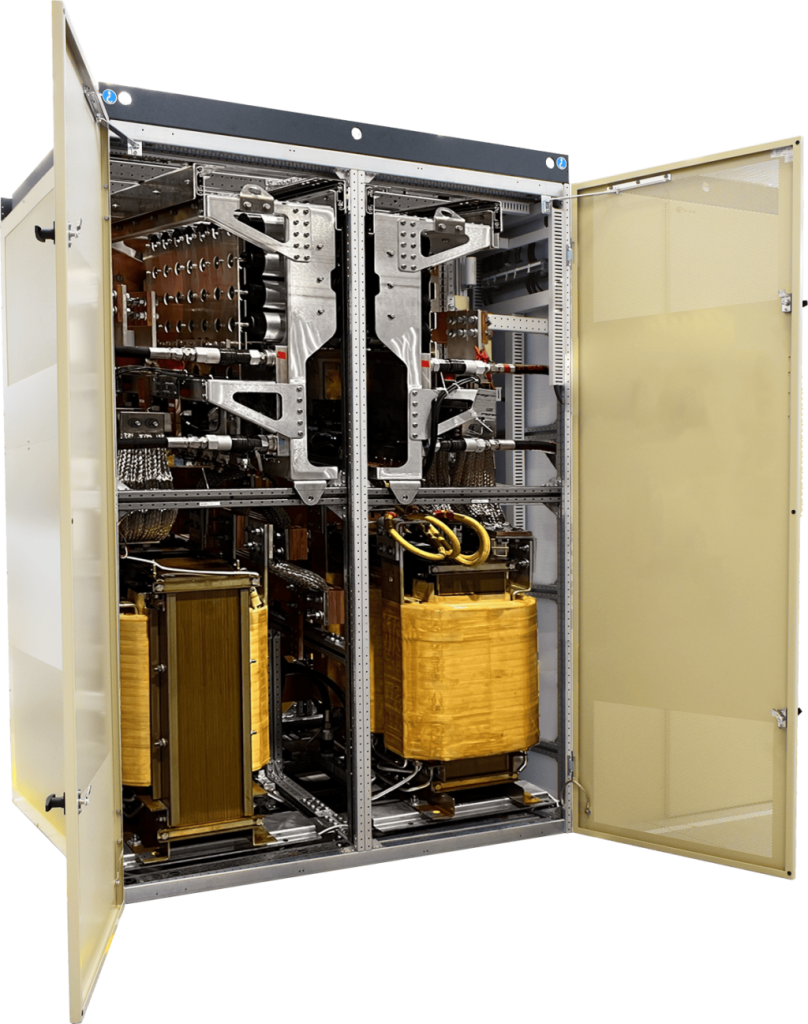
Fuente: Sécheron.
Autor:
Kumar V. Mahtani Mahtani
Profesor Ayudante en el Departamento de Automática, Ingeniería Eléctrica y Electrónica e Informática Industrial, Universidad Politécnica de Madrid.
La producción de hidrógeno a partir de la electrólisis del agua es una de las tecnologías más prometedoras en la transición hacia fuentes de energía renovables y sostenibles. Los electrolizadores, dispositivos que descomponen el agua en oxígeno e hidrógeno utilizando electricidad, requieren fuentes de alimentación de alta calidad para operar de manera eficiente. La tecnología de rectificadores juega un papel crucial en la conversión de corriente alterna (CA) a corriente continua (CC) necesaria para los procesos electroquímicos dentro de los electrolizadores. En este contexto, diversas topologías de rectificadores han sido desarrolladas para satisfacer las demandas específicas de los sistemas de electrólisis, especialmente en aplicaciones que requieren integración con redes eléctricas, eficiencia energética y fiabilidad operativa. A continuación, se describen algunas de las soluciones de rectificadores de última generación propuestas por Sécheron, que representan avances significativos en esta área.
1. Rectificador de diodos + Convertidor DC/DC: Alta eficiencia y bajo coste

Una de las soluciones más sencillas y rentables para los electrolizadores es el rectificador de diodo + convertidor DC/DC. Esta topología proporciona una alta eficiencia con un factor de potencia superior a 0,95, lo que minimiza las pérdidas de energía y mejora el rendimiento global del sistema. Al utilizar diodos como elementos de conmutación, se elimina la necesidad de ajustes de tapping en el transformador, simplificando la configuración y reduciendo los costos operativos. Además, esta configuración es adecuada tanto para sistemas de refrigeración por agua como por aire, lo que facilita su implementación en una variedad de entornos. La principal ventaja de este tipo de rectificador es su excelente relación calidad-precio, lo que lo convierte en una opción atractiva para instalaciones de electrólisis de hidrógeno de menor escala o donde el presupuesto es limitado. Aunque esta topología no ofrece la capacidad de entregar potencia reactiva a la red, es una solución sólida para aplicaciones en redes estables.
2. Rectificador IGBT + convertidor DC/DC opcional: flexibilidad y control Avanzado

Para aplicaciones más avanzadas y exigentes, como aquellas que están conectadas a redes eléctricas débiles o alimentadas por fuentes renovables intermitentes, la tecnología IGBT combinada con un convertidor DC/DC opcional ofrece ventajas significativas. Los rectificadores IGBT (Insulated Gate Bipolar Transistor) permiten un factor de potencia unitario (1.0), lo que significa que la corriente absorbida de la red es casi totalmente activa, sin generar una gran cantidad de potencia reactiva que pueda afectar la estabilidad de la red. Además, esta topología ofrece la posibilidad de entregar potencia reactiva a la red, una característica especialmente importante cuando se trabaja con fuentes de energía renovables como la solar o la eólica, que pueden fluctuar en función de las condiciones climáticas. Al igual que la topología anterior, los sistemas basados en IGBT también pueden ser enfriados por aire o por agua, lo que otorga flexibilidad a los diseñadores de sistemas. La integración de un convertidor DC/DC opcional permite ajustar aún más la tensión de salida según las necesidades del electrolizador, lo que mejora la eficiencia general del sistema y permite una mayor estabilidad operativa.
3. Rectificador de tiristores: alta corriente y potencia con refrigeración natural

Para aplicaciones de mayor escala y potencias elevadas, el rectificador de tiristores es una opción destacada. Los tiristores, a diferencia de los diodos y los IGBT, son dispositivos de conmutación controlada que permiten una regulación precisa de la corriente y una respuesta más rápida a las variaciones de carga. Este tipo de rectificador es capaz de manejar salidas de alta corriente, lo que lo convierte en ideal para electrolizadores que requieren grandes cantidades de energía continua. Además, los rectificadores de tiristores pueden operar con refrigeración natural, lo que reduce la necesidad de sistemas de refrigeración complejos y costosos. Con la posibilidad de emplear transformadores con taps, se pueden ajustar fácilmente los parámetros de salida para optimizar el rendimiento del sistema en función de la demanda de energía. Los rectificadores de tiristores pueden ser enfriados tanto por agua como por aire, dependiendo de la aplicación específica. La principal ventaja de esta tecnología es su capacidad para manejar cargas elevadas de corriente con alta fiabilidad y eficiencia, lo que es esencial para instalaciones industriales de gran escala.
Consideraciones finales
La elección de la topología de rectificador adecuada para un sistema de electrólisis depende de varios factores, como la potencia requerida, las características de la red eléctrica y los requisitos específicos de la instalación. Las soluciones de rectificadores ofrecidas por Sécheron cubren un amplio espectro de necesidades, desde sistemas de electrólisis de bajo coste y alta eficiencia hasta soluciones avanzadas que requieren flexibilidad en la entrega de potencia reactiva y capacidad para operar en redes eléctricas dinámicas. En todos los casos, el objetivo es garantizar un suministro de energía estable y eficiente que permita a los electrolizadores operar de manera óptima, contribuyendo a la producción de hidrógeno como fuente de energía limpia y sostenible.
“Rectificar es de sabios”: Subestaciones rectificadoras en transporte ferroviario electrificado en corriente continua
Autor:
Kumar V. Mahtani Mahtani
Profesor Ayudante en el Departamento de Automática, Ingeniería Eléctrica y Electrónica e Informática Industrial, Universidad Politécnica de Madrid.
Las subestaciones de tracción son instalaciones clave en el sistema de transporte eléctrico, como tranvías, metros y trenes de cercanías. Su principal función es suministrar energía eléctrica al material rodante, es decir, a los vehículos que se desplazan sobre las vías, mediante una línea aérea de contacto. Para lograr este cometido de manera eficiente, las subestaciones de tracción utilizan una serie de equipos y sistemas especializados que permiten transformar, controlar y proteger la energía eléctrica que se suministra.

Una subestación de tracción de corriente continua cuenta con varios componentes fundamentales para su correcto funcionamiento. Uno de los más importantes son los rectificadores de potencia. Estos dispositivos son los encargados de transformar la corriente alterna (CA) de la red eléctrica en corriente continua (CC), que es la forma de energía utilizada. La rectificación es un proceso clave, ya que la energía de la red suele ser alterna, pero los sistemas de tracción requieren una corriente continua estable para operar sin problemas.
Características técnicas de las subestaciones de tracción
La potencia instalada en estas subestaciones varía dependiendo del tipo de transporte. Para tranvías y metros, generalmente se emplean rectificadores de entre 1 y 3 MW, mientras que para trenes de cercanías y de media distancia se requieren potencias mayores, de entre 3 y 6 MW, debido a la mayor demanda energética de estos vehículos.
Para reducir el impacto de los armónicos (variaciones no deseadas en la señal eléctrica) en el sistema, se utilizan transformadores rectificadores de 12 pulsos. Esta tecnología disminuye el “rizado” de la tensión y mejora la calidad de la corriente continua suministrada, lo que se traduce en un funcionamiento más eficiente y menos perturbaciones en otros equipos electrónicos.
El transformador rectificador se conecta a la red de Alta Tensión a través de un sistema en triángulo y tiene dos secundarios: uno también en triángulo y otro en estrella. Esto permite obtener un desfase de 30 grados entre las tensiones y una pulsación dodecafásica, lo que mejora la estabilidad y eficiencia del sistema.

Existen diversas configuraciones para subestaciones de tracción que varían según la complejidad del sistema y la potencia requerida. Una opción simple es la subestación con un solo grupo rectificador dodecafásico, trabajando con un sistema de 1×3000 Vcc, donde un único grupo rectificador convierte la corriente alterna en continua a través de una configuración de 12 pulsos, lo que minimiza los armónicos y mejora la calidad de la energía. Esta configuración es común en sistemas de baja a media potencia, como en tranvías o metros.
En configuraciones más complejas, como las subestaciones con 2×3000 Vcc, se incorporan dos grupos rectificadores dodecafásicos que permiten manejar mayores demandas de potencia, siendo una opción ideal para trenes de cercanías o sistemas con alta carga. En estas subestaciones más avanzadas, además de los rectificadores dodecafásicos, se emplea un circuito simple con doble salida feeder, lo que permite distribuir la energía de manera más eficiente, brindando redundancia y mayor fiabilidad en el suministro.
En configuraciones aún más sofisticadas, como las subestaciones con 1 o 2 grupos rectificadores dobles de ±3 kV, el sistema permite una mayor flexibilidad y control sobre la energía suministrada, mejorando la estabilidad del sistema eléctrico al proporcionar dos salidas de corriente continua que pueden operar en diferentes polaridades. Este tipo de subestación es más adecuado para sistemas ferroviarios de alta demanda o en situaciones donde se requiera una mayor fiabilidad y capacidad de respuesta ante posibles fallos.
Los rectificadores y su funcionamiento
Los rectificadores de una subestación de tracción están formados por diodos de silicio de alta resistencia, capaces de soportar tensiones inversas elevadas y grandes corrientes. A la salida de estos rectificadores, se instalan filtros en paralelo formados por bobinas y condensadores que eliminan los armónicos, evitando que estos interfieran con las señales de comunicación y otros sistemas electrónicos.
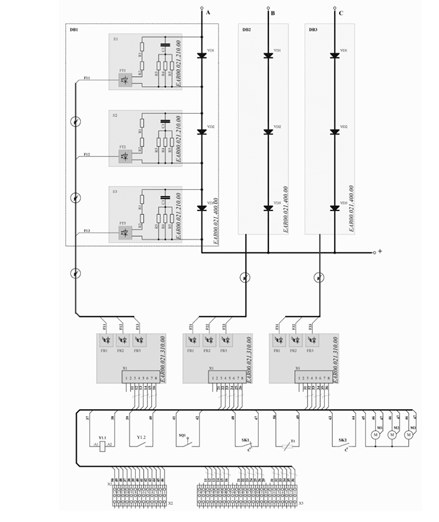
El rectificador tiene características específicas para asegurar su fiabilidad y seguridad. Entre ellas se incluyen sistemas de control para la ruptura de los diodos en caso de fallo, señales que desconectan los interruptores de potencia si ocurre algún problema en el rectificador y un sistema de enfriamiento forzado de los diodos, que utiliza refrigerantes en tubos de calor y ventiladores con frecuencia variable para mantener la temperatura adecuada. está diseñado para convertir la corriente alterna en corriente directa en las subestaciones de tracción de los ferrocarriles eléctricos actuales y del transporte urbano eléctrico. Además, las puertas del rectificador están equipadas con cerradura de bloqueo electromagnético y contactos auxiliares para controlar el estado de las mismas.
La importancia del mantenimiento y la protección
Para garantizar el funcionamiento seguro y eficiente de las subestaciones de tracción, el diseño incluye sistemas de protección y control que se activan ante fallos en los equipos o condiciones de trabajo adversas. Esto incluye sistemas de detección de fallos de catenaria, control de temperatura de los rectificadores y mecanismos de desconexión automática en caso de mal funcionamiento.
En resumen, las subestaciones de tracción son esenciales para el correcto suministro de energía a los sistemas de transporte eléctrico. Su diseño incorpora una serie de componentes especializados que garantizan la transformación, protección y control de la electricidad, asegurando que los vehículos eléctricos puedan operar de manera eficiente y segura.
Domina tu patinete eléctrico: principios del control electrónico de motores BLDC

Autor:
Kumar V. Mahtani Mahtani
Profesor Ayudante en el Departamento de Automática, Ingeniería Eléctrica y Electrónica e Informática Industrial, Universidad Politécnica de Madrid.
Los motores de corriente continua sin escobillas, conocidos como motores BLDC (por sus siglas en inglés, Brushless DC Motors), son una tecnología que ha impulsado el desarrollo de nuevas aplicaciones, desde drones y patinetes eléctricos hasta vehículos eléctricos. A diferencia de los motores de corriente continua tradicionales, los BLDC requieren un enfoque de control más complejo debido a su diseño y funcionamiento. En este artículo, exploraremos cómo funcionan estos motores y cómo se pueden controlar de manera efectiva.
¿Qué son los motores BLDC?
Un motor BLDC es un motor eléctrico en el que no se utilizan escobillas para conmutar la corriente en las bobinas del rotor. Mientras que los motores de corriente continua tradicionales emplean un sistema mecánico con escobillas para alternar la dirección de la corriente en las bobinas, los BLDC utilizan un sistema de conmutación electrónica que cambia el flujo de energía a las bobinas del estator en un orden preciso. Este sistema de conmutación es esencial para mantener el rotor en movimiento de manera eficiente y controlada.
Una de las grandes ventajas de los motores BLDC es su mayor eficiencia energética y menor necesidad de mantenimiento, ya que, al no tener escobillas que se desgasten, se reduce la fricción y el calor generado en el motor. Esto les permite operar a altas velocidades con menos ruido y vibraciones, lo que los hace ideales para aplicaciones que requieren precisión y rendimiento a largo plazo.
Los motores BLDC tienen una estructura más compleja que los motores con escobillas, aunque los principios básicos siguen siendo similares. Estos motores generalmente constan de tres partes principales: el rotor, que está compuesto por un imán permanente; el estator, que está formado por bobinas de alambre que generan el campo magnético; y el sistema de conmutación electrónica que activa las bobinas en el orden adecuado.
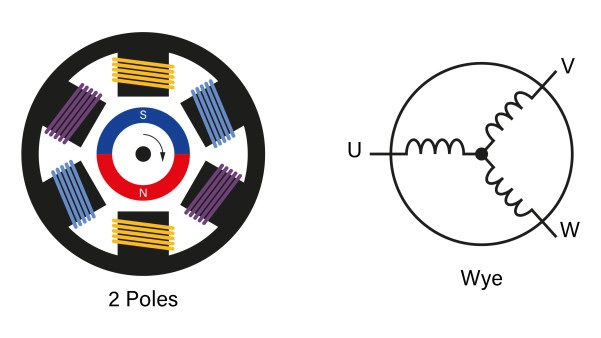
En un motor BLDC, el rotor tiene imanes permanentes que crean un campo magnético. Las bobinas del estator están dispuestas de manera que puedan generar un campo magnético variable cuando se energizan en una secuencia específica. La clave para que el motor gire correctamente es que las bobinas se enciendan y apaguen en el momento adecuado, generando un campo magnético que empuja al rotor a lo largo de su camino.
¿Cómo se conmutan los motores BLDC?
A diferencia de los motores de corriente continua con escobillas, donde la conmutación es un proceso mecánico simple, en los motores BLDC la conmutación es electrónica. Esto significa que necesitamos un sistema que controle el encendido y apagado de las bobinas del estator de manera precisa. En general, los motores BLDC operan mediante un proceso de conmutación de seis pasos, lo que implica que cada bobina se energiza en un orden específico para crear un campo magnético rotatorio que siga al rotor.

Este proceso de conmutación es realizado por un microcontrolador o un circuito integrado dedicado que gestiona la activación de los transistores (MOSFETs) conectados a las bobinas. Cada paso de la conmutación corresponde a un cambio en el campo magnético, y este cambio debe ocurrir de manera sincronizada con la posición del rotor. De no ser así, el rotor puede no seguir el campo magnético de manera eficiente, lo que generaría un movimiento errático o ineficiente.
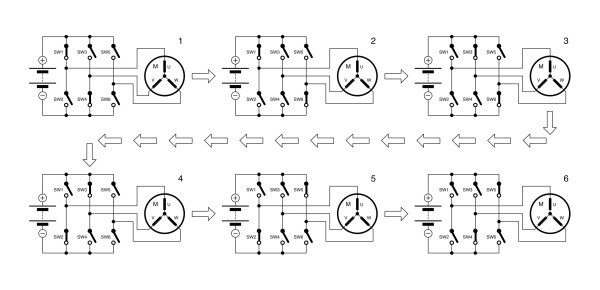
Control de la velocidad de un motor BLDC
El control de la velocidad de un motor BLDC se basa en la variación de la cantidad de tensión aplicada a las bobinas del estator. Al igual que con los motores de corriente continua tradicionales, aumentar la tensión hará que el motor gire más rápido, mientras que reducir la tensión disminuirá su velocidad. Sin embargo, dado que los motores BLDC no utilizan escobillas, el control de la velocidad requiere ajustar la frecuencia de conmutación de las bobinas, es decir, la rapidez con la que se alternan las fases del motor.

Para controlar la velocidad de manera eficiente, se utilizan técnicas de modulación por ancho de pulso (PWM), donde el microcontrolador ajusta el ciclo de trabajo de la señal PWM que se aplica a los MOSFETs. A baja frecuencia, el motor girará lentamente, y a medida que la frecuencia de conmutación aumente, también lo hará la velocidad del rotor. Esto se realiza controlando la cantidad de tiempo que las bobinas están energizadas en cada ciclo, lo que permite variar la potencia que se entrega al motor y, por ende, su velocidad de rotación.
El papel de los sensores en los motores BLDC
Una de las principales complicaciones al controlar un motor BLDC es saber en qué posición se encuentra el rotor en todo momento. Sin esta información, la conmutación de las bobinas no se puede hacer de manera precisa, lo que podría causar un funcionamiento errático o ineficiente del motor. Para resolver este problema, muchos motores BLDC incorporan sensores, como los sensores Hall, que permiten detectar la posición del rotor.
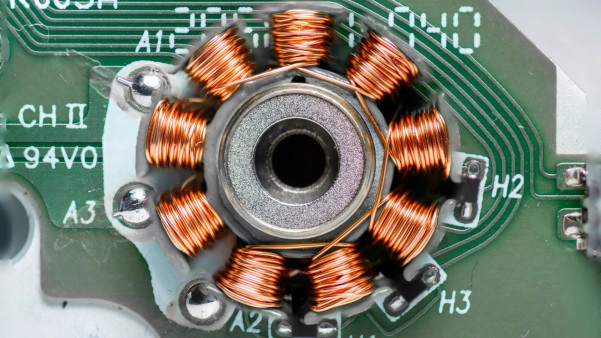
Los sensores Hall envían señales al microcontrolador que indican la orientación del rotor, permitiendo que el sistema de control decida qué bobinas deben ser energizadas en cada momento. Sin embargo, no todos los motores BLDC requieren sensores, ya que algunos sistemas utilizan la retroalimentación del motor, como la fuerza electromotriz (EMF), para estimar la posición del rotor de manera indirecta.
Conclusión
El control de motores BLDC es un tema fundamental en la electrónica moderna, especialmente en aplicaciones que requieren alto rendimiento y eficiencia, como vehículos eléctricos y drones. Aunque los motores BLDC presentan desafíos adicionales en comparación con los motores de corriente continua con escobillas, las ventajas que ofrecen en términos de eficiencia, fiabilidad y mantenimiento los han convertido en una opción popular.
Para controlar estos motores, es necesario comprender no solo su estructura física, sino también cómo se lleva a cabo la conmutación electrónica y cómo se regula su velocidad. Con el uso de controladores adecuados, sensores y algoritmos de conmutación, es posible lograr un control preciso y eficiente de los motores BLDC, lo que permite su uso en una amplia variedad de aplicaciones tecnológicas avanzadas.